Graduate Students
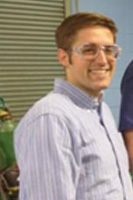
Anthony P. Ventura | Ellicott City, MD
Expected Degree: Ph.D. in materials science and engineering, 2016
Anthony continues his work with TE Connectivity, a Lehigh partner company in Harrisburg, PA. An additive manufacturing process called selective laser melting, or SLM, uses a high powered laser to melt metal powder, building parts out of many thin layers, each only 20 micrometers thick. SLM wastes little material and reduces the time it takes to develop and fabricate complex geometries, but as an emerging technology, SLM has a limited number of materials identified for its use, especially for applications that need high electrical or thermal conductivity. Anthony aims to bring copper alloys into additive manufacturing to fill this need. Early stages of the project have yielded promising results: nearly full dense (~98%) copper alloy components. Still, what is happening in the microstructure is often most important, and the severity of SLM leads to complex microstructural features. Anthony’s current efforts use electron microscopy to characterize and more fully understand the underlying mechanisms of the alloys’ properties, characterizations that may then serve as a baseline for continued adaptation of different copper alloys to SLM and expand the capabilities of the technology. Anthony has been using TE Connectivity’s SLM unit, but he describes working with Misiolek to acquire an SLM unit for Lehigh, in part with funds from the Loewy endowment, as the highlight of his year. The unit offers invaluable benefits in research leadership and education innovation.
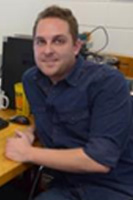
John Plumeri | Lebanon, New Jersey
Expected Degree: Ph.D. in mechanical engineering, May 2016
John works with new materials for lightweight structures, notably a new lightweight magnesium alloy with zinc and cerium additions, developing numerical models to study its behavior in a range of metal forming conditions. Numerical modeling helps develop and optimize new industrial processes without a “guess and check” stage, predicting the performance of a potential design before expensive equipment has been purchased or produced. John’s studies demonstrate that complex shapes can be produced from this material, by hot extrusion and other processes, and that the resulting properties of the parts are promising for a range of applications in automotive manufacture. Wider spread production of magnesium structures will reduce vehicle weight, fuel use, and emissions. John sincerely appreciates daily interaction with the people and topics in the IMF lab, a healthy work atmosphere that inspires excellence and a powerful sense of community. Foundation support sustains IMF’s strong group of researchers, equipment, and a diverse research portfolio that enhances members’ science as individuals and as a team.
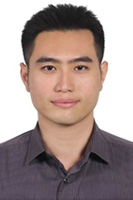
Meng Fu Huang | Kaohsiung, Taiwan
Expected degree: Ph.D. in mechanical engineering, 2018
Meng has been working with titanium alloys, specifically Ti-1023, an alloy widely used in aerospace and military applications. Improving understanding of its microstructure and mechanical properties, after laser welding and post-weld heat treatment, may help industries develop more effective and low-cost manufacturing processes. Meng takes inspiration from the visiting scholars who share their work with the IMF team. There is always something new to learn in their discussions, and excitement to share about work within and beyond the lab. For Meng, a materials engineer who can provide solutions about mechanical engineering can help make the world a better place.
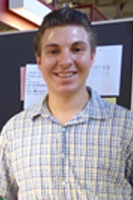
Trevor Verdonik | Butler, New Jersey
Expected degree: Ph.D. in materials science and engineering, 2018
Trevor has begun his research on the mechanical properties of metals printed on a direct metal laser sintering printer. Direct metal additive manufacturing is of interest to aerospace and defense industries as an alternative method for creating complex parts, simpler than traditional subtractive manufacturing. Among the exciting moments in Trevor’s first year with the IMF was using tensile testing equipment for the first time as well as preparing for the delivery and setup of Lehigh’s own DMLS printer. Coming from a mechanical engineering background, Trevor finds topology optimized structures particularly interesting, and has been closely following their use in aerospace. After completing his doctorate, he hopes to continue developing the science and engineering potential of additive manufacturing in aerospace or defense industries.
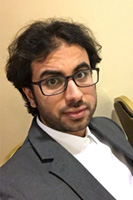
Mohammed Alamoudi | Jedda, Saudi Arabia
Expected degree: Ph.D. in materials science and engineering, 2019
Mohammed’s overarching research interest spans physical metallurgy and mechanical behavior of metals, and he currently studies the mechanisms as coarse grain structures are formed during the hot forging processing of aluminum alloys. He hopes his predictions, incorporated into numerical modeling software, will avoid undesired grain growth in the microstructure. Along with the numerical simulation, Mohammed’s research will also yield a physical model of microstructure evolution, a model that will help IMF’s automotive partner design industrial processes that achieve only its desired microstructure and targeted mechanical properties. Mohammed enjoys IMF’s bimonthly meetings. Discussing science with IMF members and distinguished visitors from all over the world in different disciplines of materials science and engineering expands his vision and develops his own knowledge. He hopes his own work in teaching or research will help transfer important knowledge and serve materials sciences’ great potential to improve society.
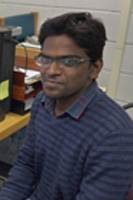
Nijenthan Rajendran | Madurai and Tamil Nadu, India
Expected degree: M.S. in mechanical engineering, 2016
Nijenthan works with continuous rotary extrusion in metal forming. Until now, most work in the area has focused on process parameters such as wheel velocity, flash gap, and abutment height. Nienthan’s work studies how the deformation zone affects process characteristics such as temperature, strain, and strain rate. An optimized numerical model for the deformation zone could improve homogeneity of the extrudate microstructure, in turn improving mechanical properties and reducing redundancies. The IMF’s many visitors, and the breadth of their research, inspire Nijenthan. He is proud to be an IMF member, and hopes to keep learning, that he might one day share what he has learned with others as a teacher and guide.
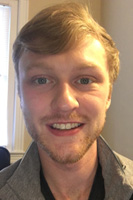
Jack Edgerton | St. Paul, MN
Expected degree: M.S. in materials science and engineering, December 2017
In Jack’s final year as an undergraduate, he was selected for the Center for Powder Metallurgy Technology’s Clayton Family Scholarship, an honor in itself, but Jack also won the award in two consecutive years. In the lab, he worked to develop a method to print electrical components using additive manufacturing. Optimizing 3-D printing could make electrical components instantly available, useful for prototyping individual parts or even entire devices. Jack’s work in the master’s program will continue to have some overlap with additive manufacturing, but will primarily explore the prevention of scale (rust) in hot-formed steel. Jack expresses overwhelming gratitude to the Loewy Family Foundation for making it possible for him to pursue higher education. It has opened a challenging and progressive future in manufacturing, perhaps in automotive, aerospace, or sports equipment.
Undergraduates
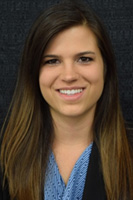
Alison Kuelz | Danville, CA
Degree: B.S. in materials science and engineering, 2015
Alison explored the porosity and surface defects in some of the cast gold jewelry created by a partner jewelry company in New York, her research supported in part by a scholarship from the Center for Powder Metallurgy Technology. Alison had never worked with precious metals, so learning how to examine and analyze them proved especially interesting. Her research helped identify and create images of the pits, and studied how powder metallurgy could improve their processes. Powders have potential to improve processing pieces in many industries, including jewelry, and Alison’s work showed that powders could greatly increase quality for this specific jeweler. Since her graduation, Alison works in industry in failure analysis, working with and learning about an exciting variety of projects and metals.
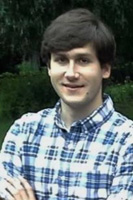
Richard Michi | Dunkirk, MD
Degrees: B.S. in materials science and engineering, B.A. in music, 2015
In his final year at Lehigh, Richard characterized the microstructures formed in a ZE20 magnesium alloy during extrusion, work that was coupled with a flow stress model developed at IMF for the same alloy. An extrusion model can inform more efficient extrusion practices, making expanded use of the alloy more attractive in the automotive industry, where its lighter weight will improve vehicle fuel efficiency. For the first time, Richard’s research results were included in a presentation at a large materials science conference, capping an exciting undergraduate experience at Lehigh. He greatly enjoyed his time performing research in the IMF, and the team was a huge help preparing him for graduate school. Richard has since begun a doctoral program at Northwestern University that segues smoothly from his explorations at IMF, and he hopes one day to earn a research position at a national lab.